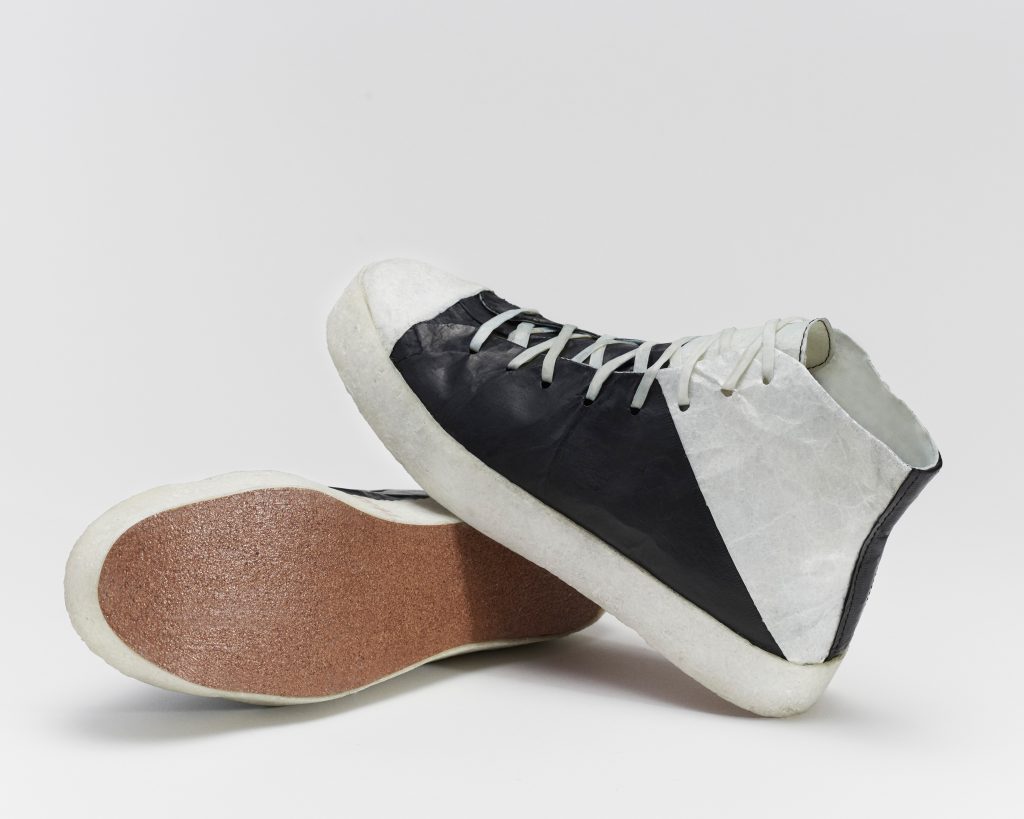
What do you get when you pair an iconic NYC streetwear brand with a materials scientist? Sneakers made entirely from waste using a process similar to making kombucha. “If that’s too difficult to understand, don’t worry. That’s how we felt at first,” explains Public School NY founders and designers Dao-Yi Chow and Maxwell Osborne on Instagram. Chow and Osborne were paired with Dr. Theanne Schiros of Columbia University and FIT as part of Slow Factory’s first science incubator, One x One. The incubator tasked teams with inventing and developing a new material that is both good for the Earth and humanity. “As we familiarized ourselves with the process and [Schiros’] studies, it’s basically everything we’d been looking for.”
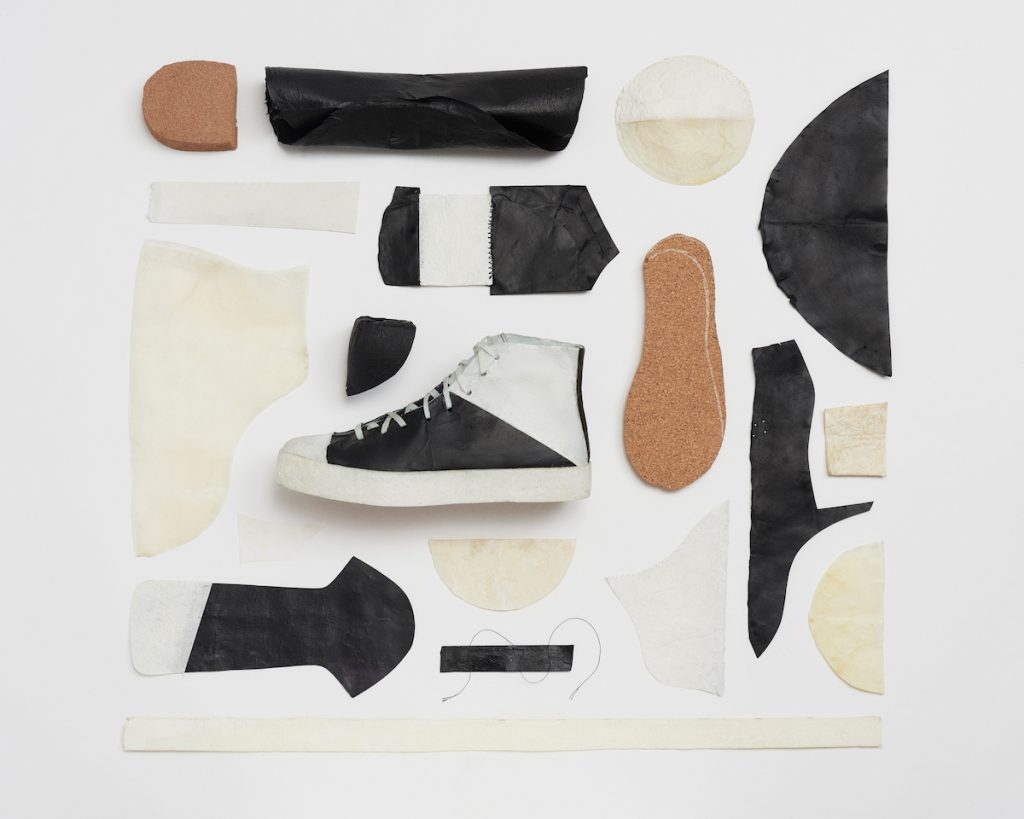
Chow, Osborne, and Schiros approached the cross-disciplinary brief intending to incorporate a naturally existing, non-toxic substitute into Public School’s usual design process. Over the years, Public School has become known for its footwear designs, ranging from sneakers to creepers. The brand often makes its shoes using real leather, which isn’t the most sustainable material out there. The result of reexamining this material choice resulted in a new “bio-leather” that challenges regular leather sourcing and production processes.
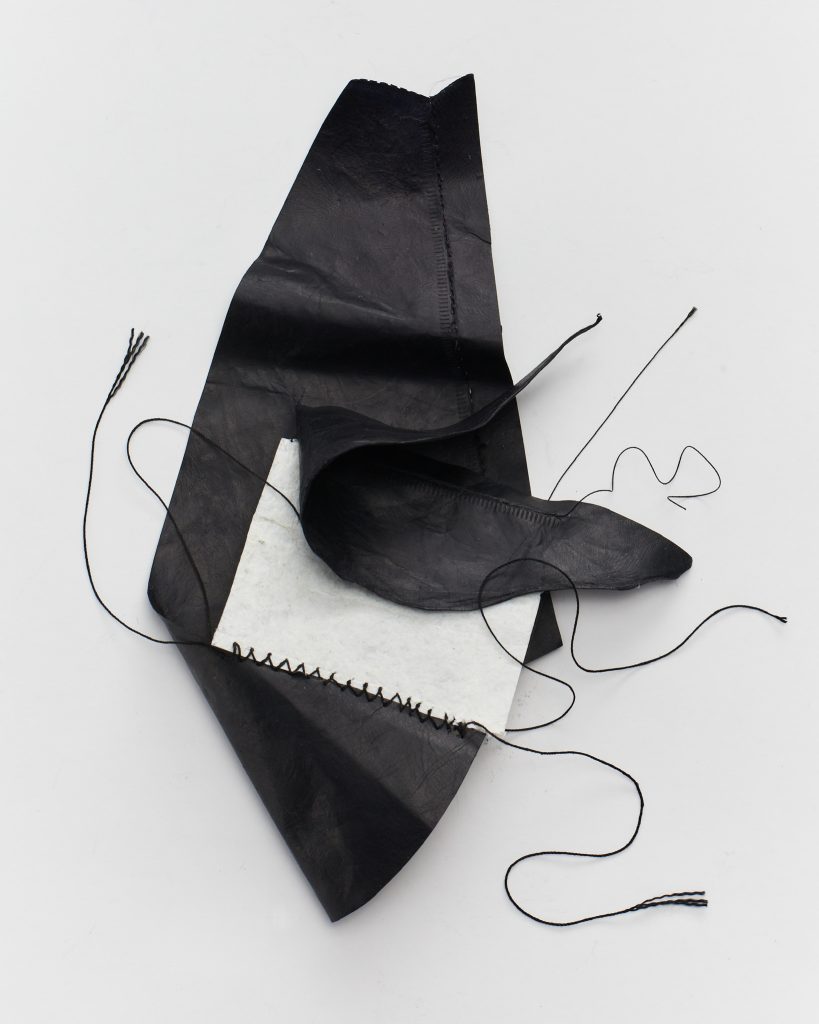
A few other sustainable leather alternatives developed by footwear brands have made headlines in recent years, including Nike’s Flyleather. However, what sets Schiros’ new cellular textile apart from the rest is that it grows naturally using the natural fermentation process used to brew kombucha, which involves a SCOBY (symbiotic culture of bacteria and yeast). “Acetic acid bacteria that produce nanofibers of cellulose as part of their metabolism have a long history in food, dating back to at least 3,000 BC and as earlier as 5,000 BC in vinegar fermentation in Egypt, and kombucha health beverages origins dating to 2000 BC in former Manchuria,” explains Schiros.
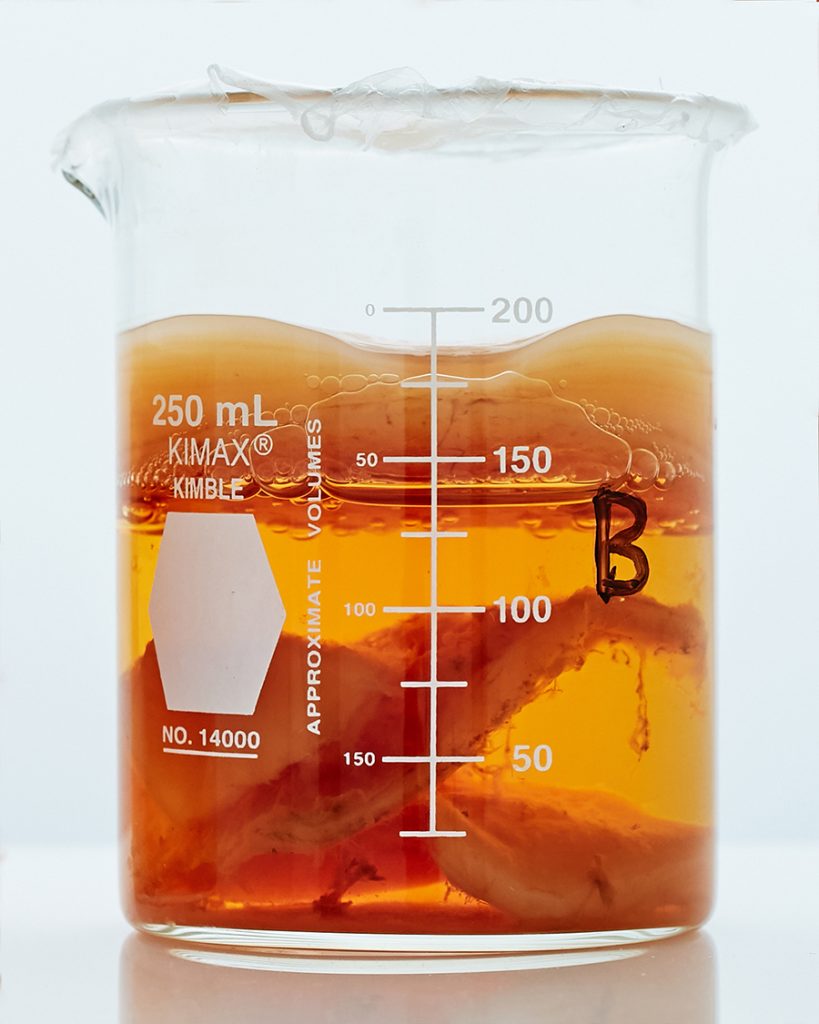
To develop the material, Dr. Schiros used two different processes: growing from scratch using a tea and sugar waste base and a circular process that involved sourcing waste SCOBY from Om Champagne Tea’s kombucha brewery.
During the waste to resource process, satisfying bubbles appear during the fermentation as the sugar gets converted into cellulose. Dr. Schiros based this process on achieving the lowest carbon and toxicity footprints possible. Dr. Schiros performed a life cycle analysis that proved that this process results in “over 10,000 times lower human toxicity than chrome-tanned leather, with 2-3 orders of magnitude lower carbon footprint than PU or plastic-based leather alternatives.”
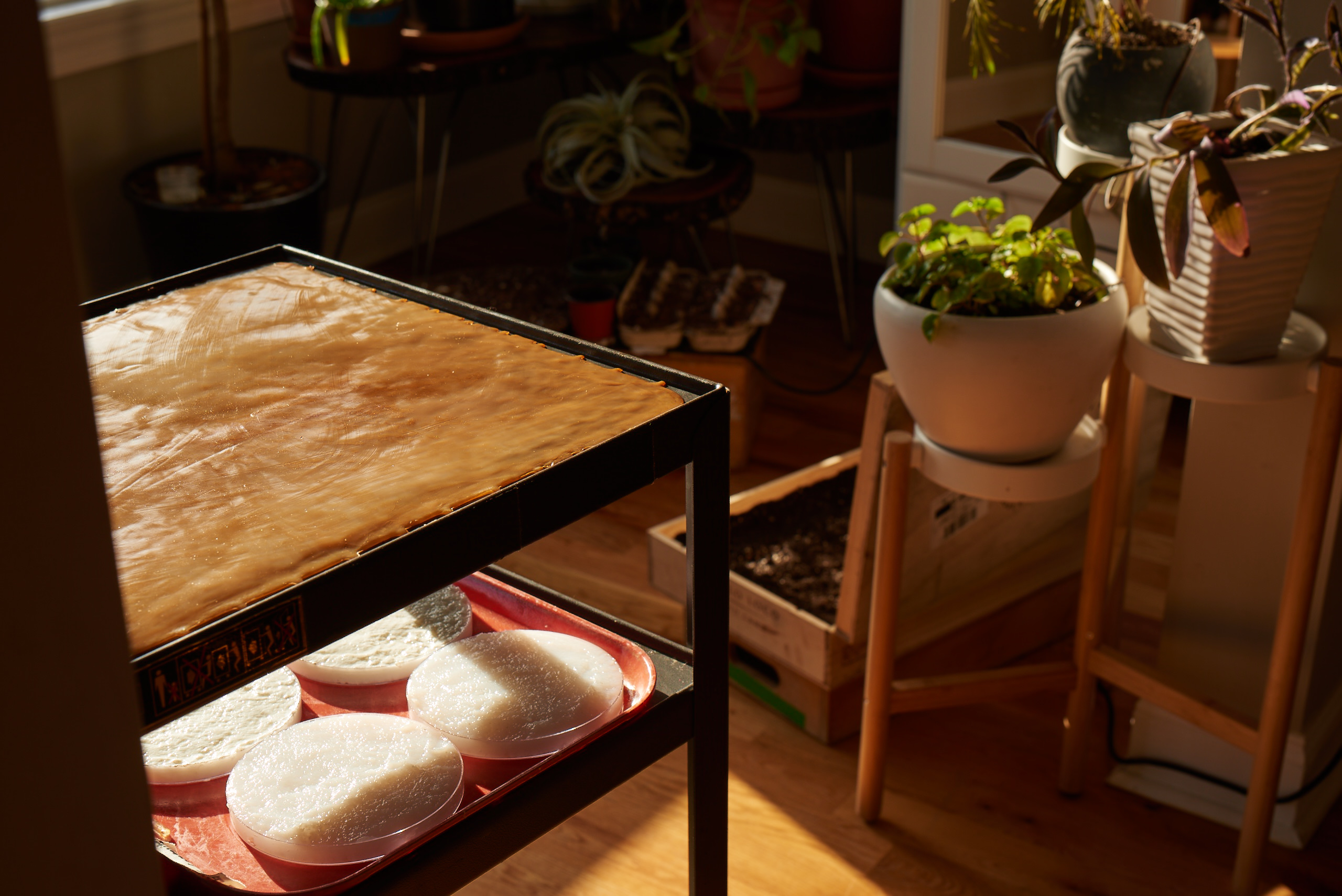
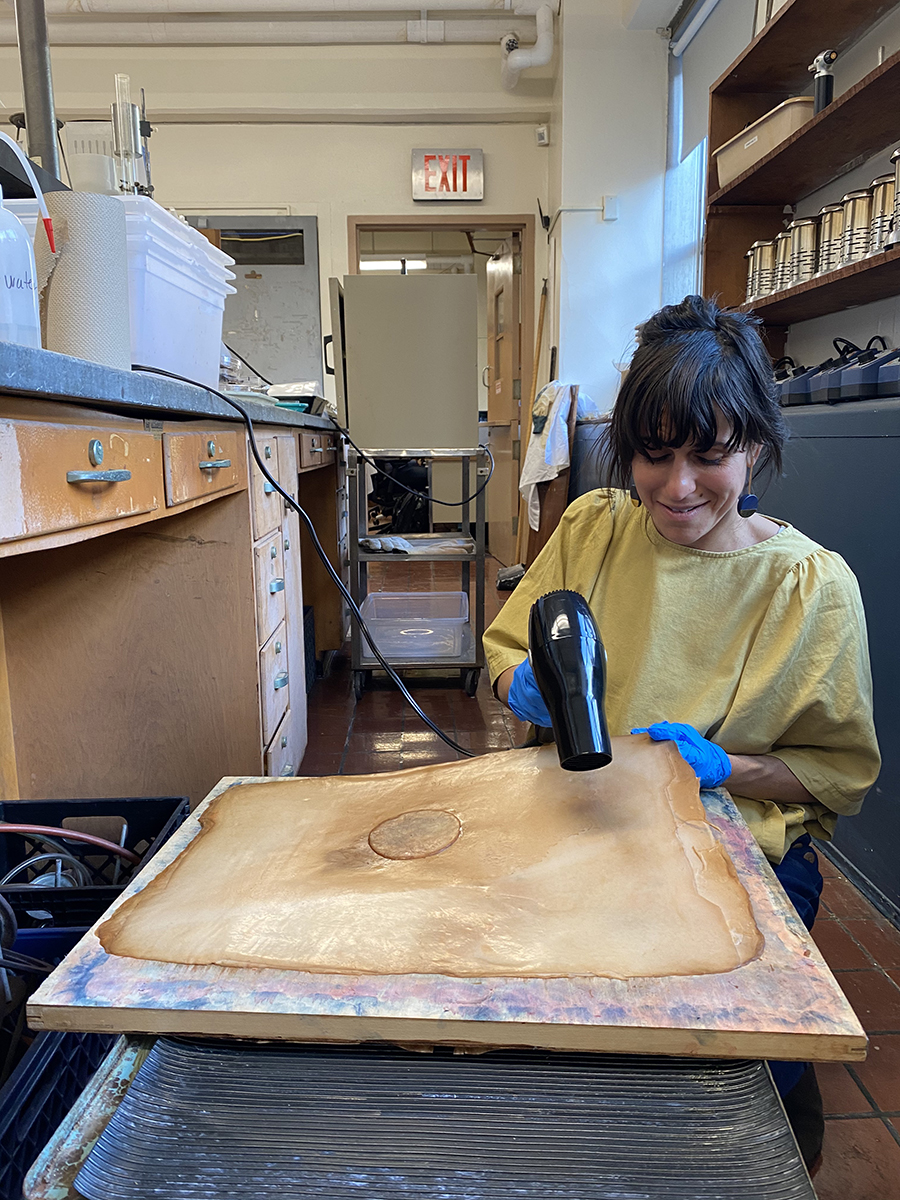
The bio-leather’s sustainable attributes go beyond its natural fermentation process. “The idea of a bacterially spun nanofiber for textile applications was wildly exciting as a regenerative material with a closed-loop life cycle,” says Dr. Schiros. Once grown, the material can shape itself to any mold it dries on top of. This molding process results in a final form that does not yield textile waste during the cutting stage. Additionally, the material can be layered with other pieces to create a seamless product. Different textures and finishes can also be achieved through various methods, including the addition of air bubbles, boiling beeswax, or laser cutting. It can even grow in color if certain types of food waste are used, such as onion skins. Oh, and it’s biodegradable.
“This was an exciting moment in circularity — and a step towards creating both regenerative materials and regenerative communities — where “waste” is an opportunity we can’t afford to miss.” – Dr. Theanne Schiros
The One x One incubator was about more than creating environmentally friendly materials — each material had to go the extra mile and fit within the matched designer’s process. “The degree of color and texture and material property exploration needed to obtain the Public School aesthetic,” Dr. Schiros explains. As a result, Dr. Schiros’ team (the bioleather was developed as a scientific partnership between Schiros, Prof. Helen Lu and Romare Antrobus of Columbia University Biomedical Engineering) created a “non-toxic tanning treatment that increased both the strength and flexibility of the bio-leather for the sneakers without compromising the material’s backyard biodegradability.” This tanning process was inspired by ancient textile techniques, such as natural tanning and dyeing.
“This was an exciting moment in circularity — and a step towards creating both regenerative materials and regenerative communities — where “waste” is an opportunity we can’t afford to miss,” continues Dr. Schiros. Learn more about Public School’s bio-leather sneakers over on One x One’s website, and watch the One x One program teaser below.