Biofabricate asks how biological materials can change the way our world is designed. Founded by Suzanne Lee, a pioneer in the world of designing biologically manufactured materials, the company’s aim is to bring together scientific innovation and systems design to re-envision how we might live in a world where the products we use and environments we inhabit can thrive symbiotically with the ecosystems surrounding us.
Earlier this year MOLD sat down with Suzanne Lee ahead of Biofabricate’s annual summit in New York. The summit spanned two days from June 6th to 7th and hosted a plethora of prototypes, panels and presentations, bringing together innovators, brands and investors to lead the transition into a “bio-made future”. Suzanne offered insight into the philosophy, culture and innovations being done with biotechnology within a diverse range of design fields and international contexts.
The ethos of biotechnology strives to change the way humans consume and relate to the material world around them by re-imagining design from a static, product-based linear process into a cyclical system that involves community, ecology and economy. Biomaterials challenge our conceptions of luxury, permanence and extraction by reframing the way in which design engages with resources and manufacturing. Suzanne Lee further clarifies this broad movement spanning across design and its implications on our present and future.
Hiba Zubairi:
What issue within the design/fashion industries brought you to biomaterials and in what ways does biotechnology address them?
Suzanne Lee:
If I go back to my early beginnings, whenre I started the project that I coined the term “bio-couture” for, I was really thinking about what the future of the fashion industry would look like and how we could do things in a different way. That particular principle goes back twenty years.
I can’t say it was sustainability that was the driving force back then because it was before the fashion industry had even become aware of sustainability. For me as a fashion designer, discovering the field of biotechnology was a design provocation of how else we might create a piece of clothing if we weren’t going to use petrochemicals, animals, or agriculture. That was my first introduction to biology as a system that could produce a material for us, more specifically, microbes, living organisms and discovering nature’s manufacturing platforms such as fungi, yeast and algae. How could we simplify the production of the material as well as the end result? Could you produce it all in one? Could we grow a dress in a vat of liquid rather than growing a sheet of material? Could you grow a shoe into its shape? Could you grow a dress into a finished garment? That was the original premise and it is still my belief that’s where we’ll end up in the future.
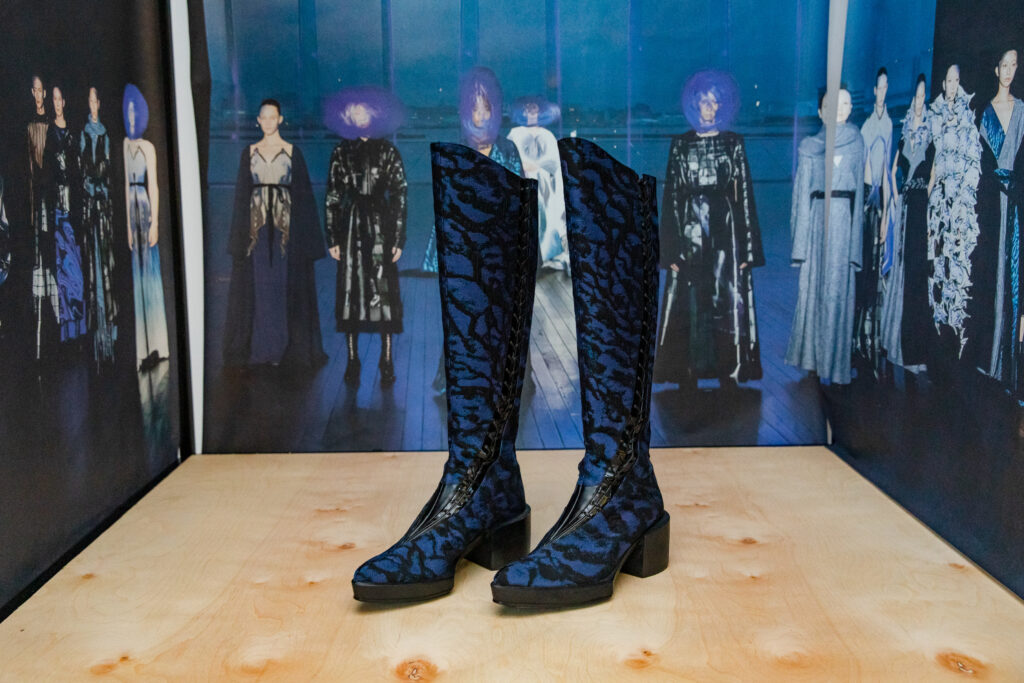
HZ:
How have you seen the innovators you work with use those processes to change the products they make? And how do their customers relate to the products they’re buying?
SL:
I was growing these materials 20 years ago, I don’t do that anymore. The foundational work and research I did was before its time. Everyone thought I was completely crazy. The idea of using a microbe-like bacteria or yeast to produce a fashion fabric had an ick-factor associated with it. Brands and investors didn’t understand it as a potential new material. We’re past that and in a very different world. I stopped growing those materials because I was 20 years too early but the Bio-Couture project exploded into a global movement. Now there are multiple companies who are using kombucha as a base for producing leather-like material. Some of the companies in this space have gotten the production time down to a few days, under a week, sometimes 2-3 days. The production, speed and efficiency has been accelerated over time.
In terms of how that gets communicated to their customers, it’s important to remember this is a very new process for material producers and brands who are using that material. What’s interesting from a design perspective is the need for new language in terms of how we discuss and describe these materials. What we’ve seen so far is that people are relying on pre-existing language: “It’s similar to animal-leather.” They’re trying to find analogies to existing materials which are not very helpful. If all we’re trying to do is replace plastic with something that looks similar, or animal skin with a mock of it, it s leaves so much creativity on the table. If you free up your mind to what nature is able to produce in terms of material properties, aesthetics, functionality and how it fits into a lifecycle, there’s so much opportunity beyond just trying to replicate pre-existing materials. That is a conversation we’re very excited about at BioFabricate. It’s a conversation the design community can have with biotechnology – what can we do as designers beyond copying these flawed materials of the past? How do we listen to the biology as we work with and begin to understand these living systems? What is that they are best suited to? We need to create a new material language, not one which mimics previously existing terms.
HZ:
What possibilities can biomaterials offer product and lifestyle design? How can we shape this culture with this emerging field of biotechnology?
SL:
There’s a big piece of education that needs to happen— to the designer, the brands and the consumer. [It is necessary] to try and encourage people to open their minds to be receptive to the look, feel and life cycle of biomaterials or biological products. When you look at a tree, every leaf will be different so why do we go into a store and expect a pair of shoes to be exactly the same as the one next to it? In contrast, that difference is what we celebrate in the natural world. Same can be applied to very high luxury. If you buy a handmade, beautiful leather bag, over time it will develop a patina, it will soften, it will change shape and all of these properties are actually what start to imbue it with value. There’s a provocation there to encourage people to think, what if the aesthetic between one product and the next was used to celebrate biodiversity rather than force biology to look like a petrochemical, uniform product.
These are challenging questions because we’re dealing with global supply chains where brands will have a standard set of targets a material must meet. That’s a barrier to a lot of innovators right now. It’s very challenging to get a material to perform the same as those which are essentially plastic. Synthetic materials are very high performing but the problem with them is we can’t get rid of them, they don’t break down. Building temporality. The way biology grows, has a function, and then composts and feeds back into a system. Embracing that into our product life cycles is vital. There’s a tension right now between existing production methods and consumption behavior, and where biology and bio-design wants to lead us. It’s going to take time and we’re not there yet. We’re at this point where these materials are starting to scale their production and they’re starting to show up in stores. It is hard for these innovators because they are being held to the same standards as materials which have had decades to reach those levels of performance, endurance and production scale. We’re putting so much expectation and pressure on people who are innovating incredibly novel systems with biology. It’s never been done before.
HZ:
Many of the innovators you’re working with are working with things such as waste and there’s so much value in that temporality. Within the processes you’ve engaged with through your work, what are some of the most rewarding and challenging conclusions you’ve experienced? What have you learned about yourself or the industry through them?
SL:
Waste is a problematic word in its own right. The economics of biomaterials are challenging when you put them up against petrochemicals, animal or intensive agricultural farming. These are all economies which have reached scale. With biology, it will become critical that the inputs are as cheap, if not free, as possible, so that you can try and keep the cost down in order for them to be competitive. The way many people are doing that is by turning to free raw material streams such as waste from the food industry or looking to waste from agriculture and so on. Looking for a low cost input your bacteria can feed on so we can work towards a circular system. We have many companies who will be presenting at the summit which are working with unorthodox raw material streams.
Like Hide Biotech, who are from the UK and are using fish collagen to make “leather”. At BioFabricate we have a holistic view. We are not vegan because we try to think of a much bigger picture which takes into account a local system along with all its inputs and outputs before we make a judgment about whether something is good or bad, and what is truly sustainable and what is truly responsible. Now with Hide for example, they use fish collagen to make a leather alternative, meaning it’s still an animal product however it’s helping to deal with a huge waste problem within the fishing industry by finding a use for that collagen.
If you look at TOMTEX who are based in New York, they are doing something very similar with shellfish. All of these natural proteins are brilliant in their own right so if you can break them down and create a sheet material or a fiber or a yarn, there’s so much you can do with that. TOMTEX not only uses shellfish, they also use coffee grounds.
Polybion in Mexico are using waste from the food industry to feed the organism in order to make sheets of bacterial cellulose.
There’s Geltor who are using microbes to make collagen for food rather than using a plant. There are many companies in this space who can use waste from the food industry as the feed stock for their material. Whether that is literally feeding another organism or breaking down that material for formulate another one. It makes so much sense because it’s a low-cost input which allows you to get cost competitive with other materials.
HZ:
It brings me back to what you were saying at the beginning about the variety of biomaterials which have a plethora of applications across industries.
SL:
There’s one I would love to share with you, it’s an architectural firm actually. It’s one of the talks I’m looking forward to at the summit. Redhouse Studios is an architectural practice that is working with NASA on a project in Namibia. They’re harvesting an invasive plant species in Namibia to use as biomass to grow mushrooms. The mushrooms are intended to invigorate the local economy by being sold, since they are a valuable crop, and feeding the community. The feed stock created by the mushrooms are filled with mycelium which the firm is using to build bricks and build structures for the community. These bricks can ultimately be broken down to feed the soil and grow food for the community once again.
It’s this incredible circular system which can come about when you design with biology, work with living systems, and they’re thinking about not just food but materials, construction and addressing a local environmental problem such as a local invasive species. It’s a great example of how you can work with nature and biology to support people and grow food.
HZ:
We’re talking about material and biological processes but this also becomes a human intervention which gives back to the community in so many different ways and phases. In thinking about it as a system, it relates to people as a relationship not a product.
SL:
It’s important we support this work in places which are not abundant with resources. How can these processes work where you don’t have access to fancy labs and infrastructure? Are there skills which can be taught to the local community to advance their own technology which works within the cultural context?